Navigating the world of high-density slurry pumps requires a blend of expertise and experiential insights. At the heart of industries like mining, oil, and wastewater treatment, these pumps play a crucial role in handling abrasive and viscous fluids. Understanding how to optimize their use can dramatically impact efficiency and operational costs.

High-density slurry pumps are designed to handle slurries with solid concentrations averaging 20% to 40%, though some models can manage up to 70% solids. The pump's capacity to move this dense mixture efficiently without clogging or wearing out is crucial for maintaining continuous operation. This means selecting the right pump for your needs hinges on understanding its components and the environmental factors at play.
From an expert's perspective, material selection for pump construction can't be overstated. Pumps must resist abrasion and corrosion while maintaining structural integrity over time. High-chrome alloys and rubber linings are often employed in wet end parts design to extend pump longevity. This ensures that the pumps function continuously under rigorous conditions, reducing the need for frequent replacements and minimizing downtime.
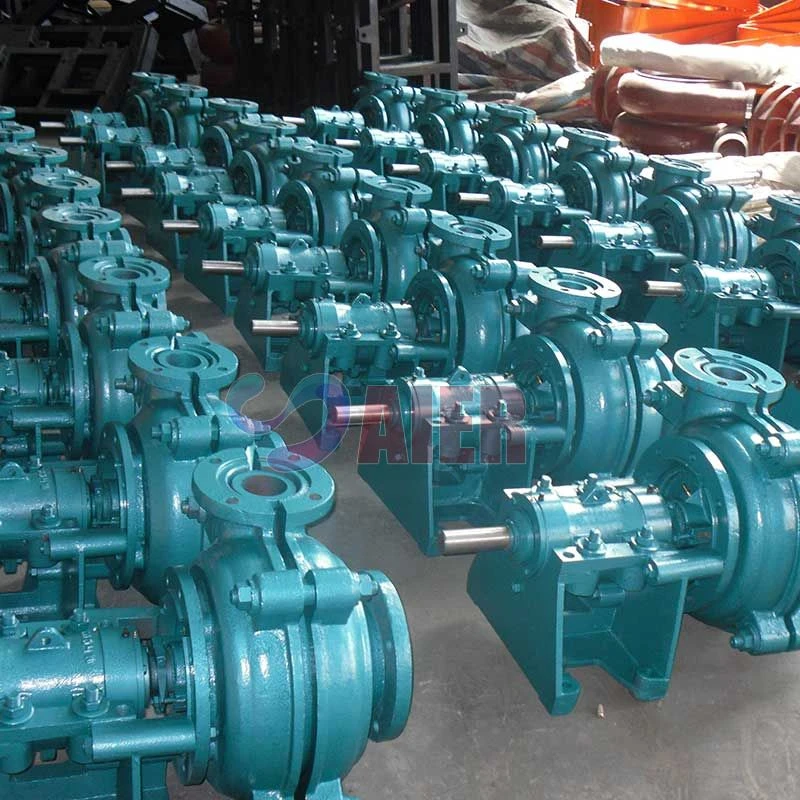
Moreover, operational expertise is essential for maximizing the efficiency of high-density slurry pumps. The specific speed or performance characteristics determined during the design phase can significantly influence their suitability for different applications. For instance, understanding the relationship between the head (the height the pump can raise a liquid) and flow rate is critical. High-density slurries often require specialized pumps that balance these factors to prevent cavitation—a damaging condition where vapor bubbles form in low-pressure areas within the pump.
Authoritativeness in selecting the right high-density slurry pump is also dictated by understanding pump hydraulics and the nature of the slurry itself. When managing non-Newtonian fluids that don't behave like simple liquids, it's vital to consult with or employ engineers versed in fluid dynamics and rheology. This ensures the chosen pump matches the demands of the slurry's viscosity and particle size distribution.
high density slurry pump
The potential environmental impact of slurry handling further accents the necessity for trustworthiness in pump selection and operation. Responsible slurry management implies ensuring that leaks, spills, and inefficiencies are minimized. Innovative designs now offer mechanical seals and auxiliary systems that help protect against environmental hazards, ensuring compliance with stringent regulations.
Investing in regular maintenance and real-time monitoring solutions also bolsters trustworthiness. Predictive maintenance technologies, like vibration monitoring and thermography, aid in early detection of wear and potential failure points, allowing for timely interventions. Coupled with AI and machine learning, these technologies can predict the remaining service life of pump components, enabling data-driven decision-making to prevent unexpected breakdowns.
Finally, considering total lifecycle costs rather than just the initial purchase price is crucial in acquiring high-density slurry pumps. This holistic approach includes evaluating energy usage, maintenance costs, availability of spare parts, and the ease of maintenance accessibility. By focusing on long-term performance and reliability, businesses can ensure they’re leveraging their investments for sustained operational excellence.
In conclusion, the integration of experiential insights, expert knowledge, and authoritative applications in the realm of high-density slurry pumps guarantees their role as indispensable assets in industrial operations. Through meticulous selection, material considerations, and environmental awareness, these pumps offer dependable solutions that uphold ecological standards while maximizing industrial performance.