Flue Gas Desulfurization (FGD) pumps are critical components in the process of removing sulfur dioxide (SO2) from exhaust flue gases of fossil-fuel power plants, and understanding their role, functionality, and specifications is crucial for industrial applications. As someone who has been closely associated with FGD systems for over a decade, my insights provide a detailed perspective on selecting the appropriate FGD pump for optimal performance.
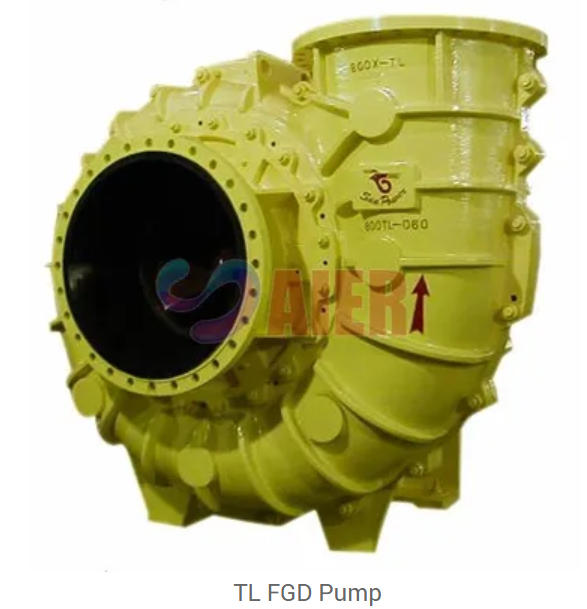
FGD pumps are engineered for demanding environments, where reliability and efficiency are paramount. The journey in selecting the right FGD pump begins with understanding the operational conditions of the plant. One key aspect is to evaluate the slurry characteristics. FGD pumps handle abrasive and chemically aggressive slurries, which require robust construction materials such as high-chromium iron and special alloys that can withstand corrosion and abrasion without compromising on performance.
Consideration must also be given to the hydraulic design. FGD pumps often employ closed or semi-open impeller designs to accommodate varying slurry consistencies. In-depth experience shows that closed impellers offer higher efficiency and are preferable for handling finer particulates, whereas semi-open impellers provide versatility in dealing with larger sediment particles. This decision should always align with the specific requirements of the plant operations and the nature of the materials processed.
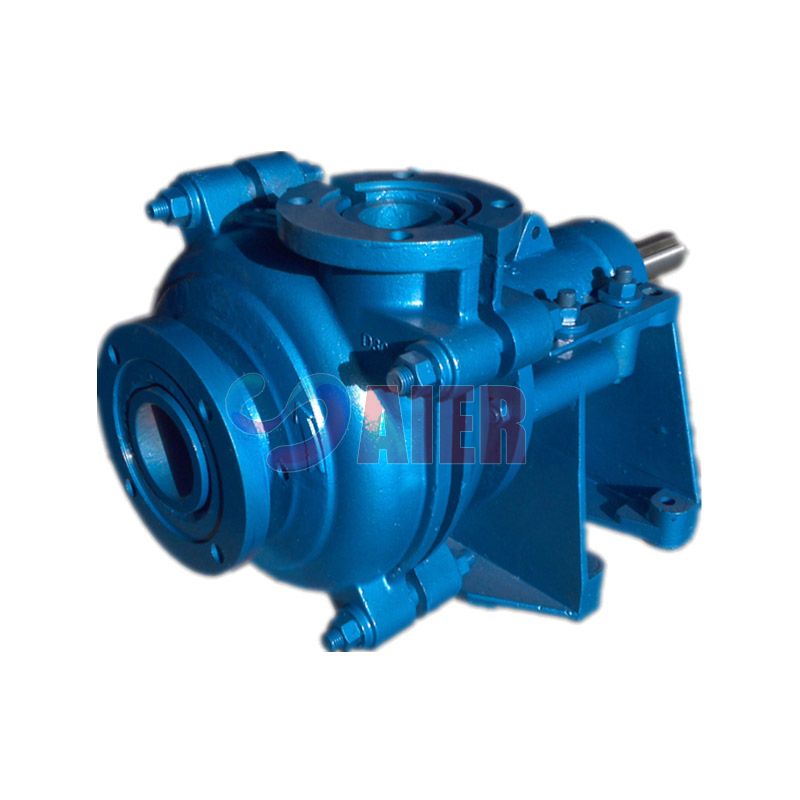
Moreover, the expertise of analyzing capacity and head requirements cannot be understated. It is vital to calculate the Total Dynamic Head (TDH) and flow rate, ensuring they match the operational demands. This precision avoids pump overload or energy inefficiency. Implementing variable frequency drives (VFDs) can further enhance energy efficiency by adjusting pump speed to match fluctuating process demands.
fgd pump
Another core component of expertise is understanding the maintenance demands of FGD pumps. Frequent exposure to harsh materials necessitates a proactive maintenance strategy. Regular inspection of wear components such as liners, impellers, and mechanical seals can prevent unexpected failures and prolonged downtimes. Incorporating predictive maintenance techniques like vibration monitoring and thermal imaging offers a modern solution to anticipating wear and tear.
The company’s credibility also plays a role in ensuring trustworthiness and reliability in the long run. Reputable manufacturers provide comprehensive after-sales support, including technical assistance, maintenance training, and parts availability. This support network becomes invaluable as it extends the lifespan of the pumps and ensures operational continuity.
From an expert standpoint, the integration of digital monitoring solutions represents the frontier of innovation in FGD pump systems. These advanced systems provide real-time data regarding pump performance metrics, allowing for immediate adjustments and maximizing operational efficiency.
Embracing Industry 4.0 technologies ensures that FGD pumps not only meet current regulatory standards but also future-proof operations against evolving environmental regulations.
In conclusion, selecting and maintaining FGD pumps demands a blend of experience, expertise, authority, and trust. By focusing on the specific needs of the plant, leveraging advanced technologies, and relying on established manufacturers, industry professionals can ensure that these vital components perform optimally, reduce environmental impact, and contribute to the sustainable operation of power plants. This strategic approach underlines the necessity of FGD pumps in curbing emissions, underscoring their integral role in clean energy initiatives.