When it comes to the manufacturing of slurry pump parts, precision in casting is crucial to ensure durability and performance. Slurry pumps are essential in industries such as mining, dredging, and industrial wastewater treatment, where they handle abrasive, high-density slurries. The casting process for slurry pump parts must be meticulous, as these parts frequently encounter harsh environments that test their limits.
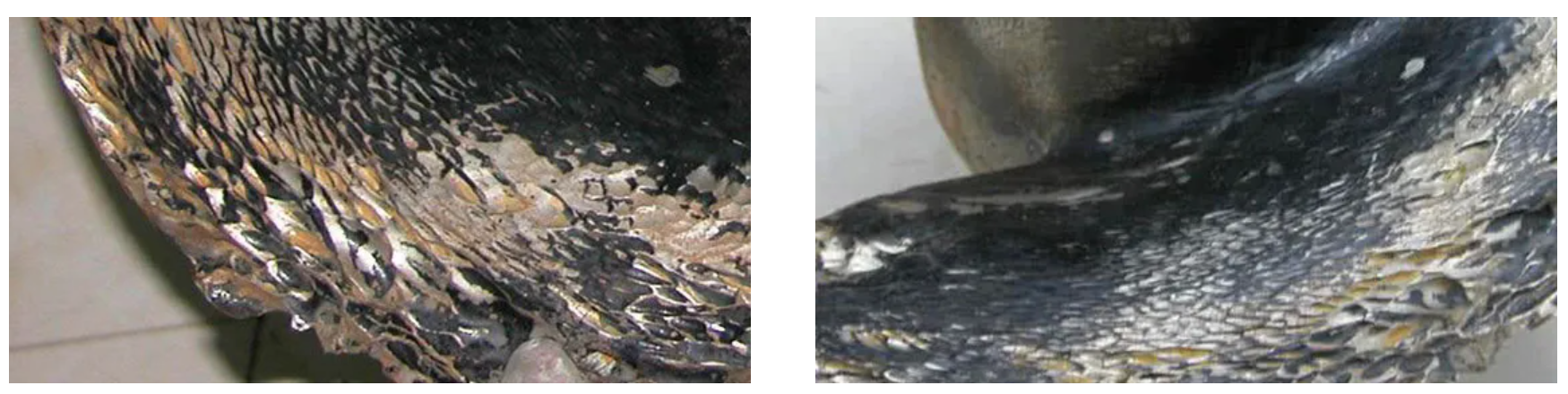
Experience reveals that the selection of materials is the initial step in ensuring that slurry pump parts withstand the demanding conditions they are exposed to. High-chrome alloys, ductile iron, and rubber-lined castings are popular choices, each with specific advantages. High-chrome alloys are revered for their hardness, making them ideal for high-abrasion applications, while ductile iron offers excellent toughness, and rubber liners provide resilience against corrosion and abrasion.
In the realm of expertise, the casting process is a blend of science and art. It begins with designing precise patterns and molds, which are foundational to creating accurate and reliable components. Advanced techniques such as computer-aided design (CAD) and rapid prototyping are employed to model and perfect these designs before they proceed to production. Additionally, simulation software predicts and mitigates potential defects within the final product, ensuring consistency and quality throughout the casting process.

As an authority in the field, manufacturers must adhere to rigorous quality control protocols. Testing methods such as hardness testing, dimensional inspection, and non-destructive testing (NDT) are standard practices to evaluate the metallurgical properties and dimensions of the cast parts. This commitment to quality not only guarantees superior performance but also establishes the firm as a trusted name in the production of slurry pump parts.
casting slurry pump part
Trustworthiness is built through a transparent manufacturing process that instills confidence among clients. Transparency involves not merely straightforward communication but also showcasing the processes that go into manufacturing superior products. Providing detailed technical documentation and comprehensive testing reports plays a critical role in affirming a manufacturer's commitment to quality and reliability.
Modern manufacturing facilities incorporate sustainability practices in producing slurry pump parts, aligning with global environmental standards. Waste reduction, recycling of materials, and energy-efficient operations are prioritized to minimize environmental impacts, thereby enhancing the company's reputation as a responsible manufacturer.
Customer feedback loops and continuous improvement initiatives ensure that experiences are optimized and expertise is constantly expanded. Listening to clients' operational challenges and evolving requirements allows manufacturers to innovate and refine their products, addressing specific needs effectively.
To summarize, the casting of slurry pump parts is an intricate process that demands technical expertise, strict quality control, and a commitment to sustainability. Industry leaders distinguish themselves by their ability to deliver high-quality, reliable products through a transparent and environmentally-conscious process. These factors contribute to their reputation, making them trustworthy partners in industries where performance and resilience are non-negotiable.