In the intricate world of industrial slurry transportation, the dredge pump impeller stands as an unsung hero. As the heart of the dredging pump, it transforms hydraulic energy into kinetic energy, enabling the movement of slurries with efficiency and precision. Understanding the significance of this component begins with recognizing its role and the factors influencing its selection, performance, and maintenance.
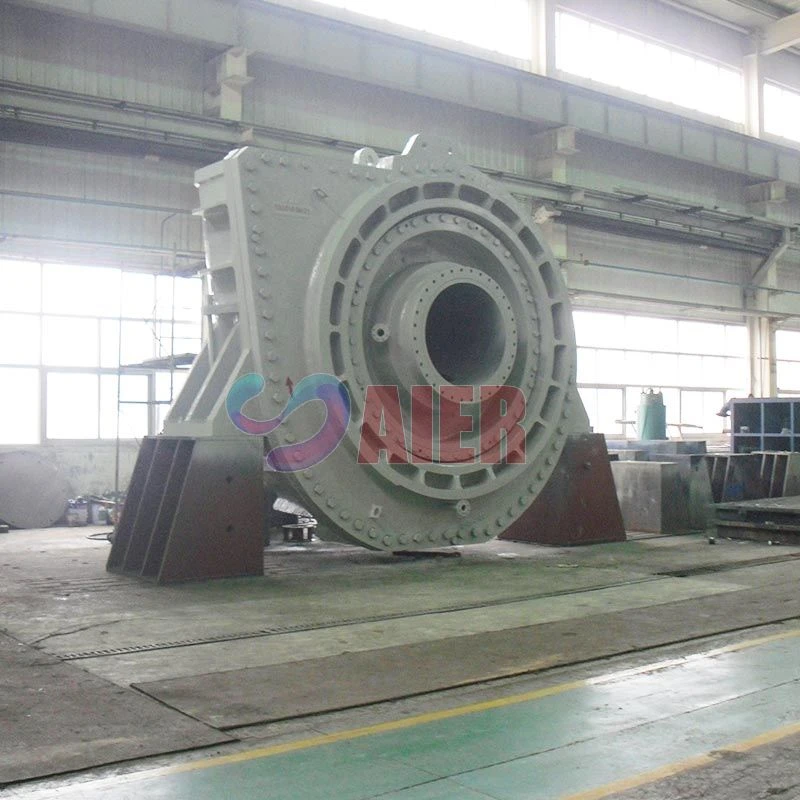
The impeller's primary function is to convert rotational energy, often supplied by a motor, into fluid flow. It achieves this through a careful balance of its size, shape, and material—factors that directly impact the overall efficiency of the pump system. Given its critical function, selecting the right impeller design is paramount to optimizing operations and prolonging the lifespan of the equipment.
Among the various types of impellers, open, semi-open, and closed designs each serve distinct purposes. Open impellers are preferable for applications where blockages from debris are a concern, while closed impellers offer superior efficiency due to their more complex structure. Semi-open designs strike a balance between the two, offering moderate efficiency and blockage resistance. Each choice is influenced by the intended application, fluid characteristics, and operational priorities.
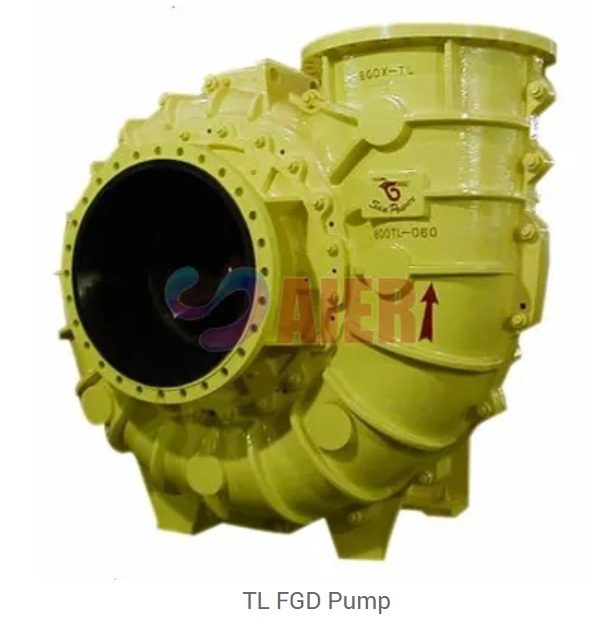
Materials are equally crucial in determining an impeller's longevity and effectiveness. Abrasive-resistant materials such as high-chrome iron or rubber-lined impellers are vital for enduring the harsh conditions of grueling dredging operations. Not only do they resist wear and tear, but they also minimize downtime and maintenance expenses. Selecting the proper material ensures reliability, especially in operations that involve harsh and abrasive materials like sand, gravel, or rocks.
dredge pump impeller
For those invested in the successful operation of dredge pumps, understanding the nuances of impeller design and function goes beyond mere selection. Regular maintenance is a necessity, as even a well-chosen impeller requires periodic inspection and recalibration to maintain its performance. Inspecting impellers for signs of wear, erosion, or cavitation ensures that any issues are addressed before they escalate into costly repairs or replacements.
Innovations in impeller technology continually push the boundaries of what is possible, offering solutions that enhance both performance and efficiency. Computational fluid dynamics (CFD) simulations have revolutionized impeller design by allowing engineers to predict flow patterns and optimize impeller geometry accurately. These advanced models help reduce energy consumption while maximizing the conveyance capacity of the slurry, aligning with contemporary demands for sustainable and cost-effective industrial operations.
The future of dredge pump impellers leans toward enhanced customization and adaptability. Considerations such as impeller trimming, where the impeller diameter is adjusted for precise flow specifications, demonstrate a shift toward tailored solutions. This adaptability is crucial in industries where pump systems must adhere to evolving operational demands and regulatory conditions.
Ultimately, the sophistication of the dredge pump impeller underscores its vital role in dredging operations. By prioritizing expertise in selection, ongoing maintenance, and adopting cutting-edge innovations, industry professionals can ensure the integrity and efficiency of their dredging projects. The journey from selecting an impeller to its eventual integration is marked by comprehensive knowledge and strategic foresight—a testament to the importance of experience, expertise, authority, and trust in the complex domain of dredge pump systems.