In the world of industrial applications involving the transportation of abrasive or corrosive slurries, the choice of pump components can significantly impact performance and longevity. As one of the most integral components, the gland seal of a Warman slurry pump is often overlooked, yet it plays a crucial role in ensuring operational efficiency and reliability.
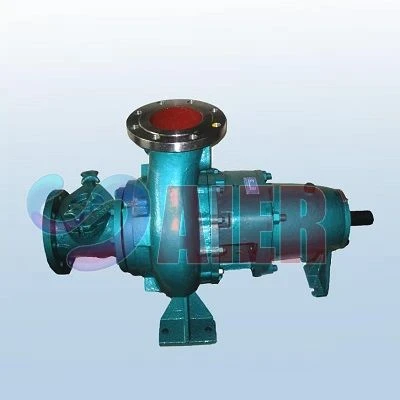
A majority of industries rely on slurry pumps for the transportation of solids in water. Applications range from mining and mineral processing to chemical processing and wastewater management. In all these applications, the effectiveness of the pump's gland seal determines how well the equipment can handle tough slurries without excessive wear and tear or leakage.
The gland seal in a Warman slurry pump serves as a critical interface between the moving parts of the pump and the stationary housing. Its main function is to prevent slurry or water from leaking out of the pump housing along the shaft. If the seal fails, it can lead to operational downtime, equipment damage, and increased maintenance costs. Thus, a sound understanding of Warman's gland seal operations is essential for optimizing any industrial slurry pumping process.
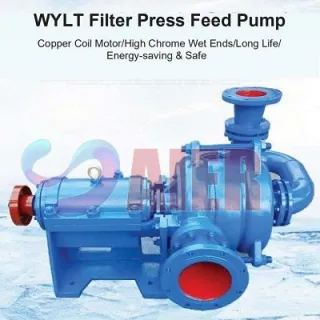
One of the most significant advantages of using a Warman slurry pump gland seal is its adaptability in various environments. Crafted with high precision, these seals are designed to endure the harshest of conditions while maintaining an impeccable sealing function. Industries often encounter fluctuating pressures and temperatures, making it imperative for the seal to perform consistently. Warman's gland seals, thanks to their robust design, adapt well to these changes, mitigating the risk of leaks and ensuring longevity.
Another key feature of Warman slurry pump gland seals is their contribution to energy efficiency. Seals that perform optimally reduce the loads on moving components, thereby minimizing energy consumption. This not only lowers operational costs but also aligns with green initiatives aimed at reducing the environmental footprint of industrial operations. By choosing Warman’s high-quality gland seals, companies can effectively decrease energy use and promote sustainable practices.
warman slurry pump gland seal
Expert reviews and user experiences highlight the ease of maintenance associated with Warman slurry pump gland seals. Unlike other seals that require frequent adjustment and monitoring, Warman seals are designed for minimal intervention. This is particularly beneficial in industries where downtime leads directly to loss of productivity and revenue. The reliability of these seals translates to confidence in continuous operation, further emphasizing their trustworthiness in critical applications.
Expertise in slurry handling technologies reveals that the primary reason for Warman's leadership in this domain is its commitment to innovation and quality. The precision in manufacturing and material selection ensures each gland seal meets the strictest industry standards. Engineers and technicians acknowledge that the use of advanced materials and cutting-edge technologies in these seals significantly extends the service life of the pump, thus reducing long-term operational expenses.
Warman’s reputation for excellence in slurry pump technology is not only underpinned by its commitment to product quality but also by its extensive support network. Access to a wealth of knowledge from their experienced engineers provides users with the necessary guidance to maximize the performance and life of their slurry pumps. This aspect of trustworthiness in customer support positions Warman as a leader in the pump industry.
In summary, the Warman slurry pump gland seal is an embodiment of reliability, efficiency, and adaptability in the realm of slurry transportation. For industries striving for enhanced productivity, reduced operational costs, and commitment to sustainability, Warman provides an unparalleled solution. The longevity and performance stability of these gland seals attest to Warman's promise of quality and efficiency, making them an indispensable component in industrial slurry handling systems.