Rubber Lined Slurry Pump Spare Parts Unveiling the Essentials for Optimal Performance and Longevity
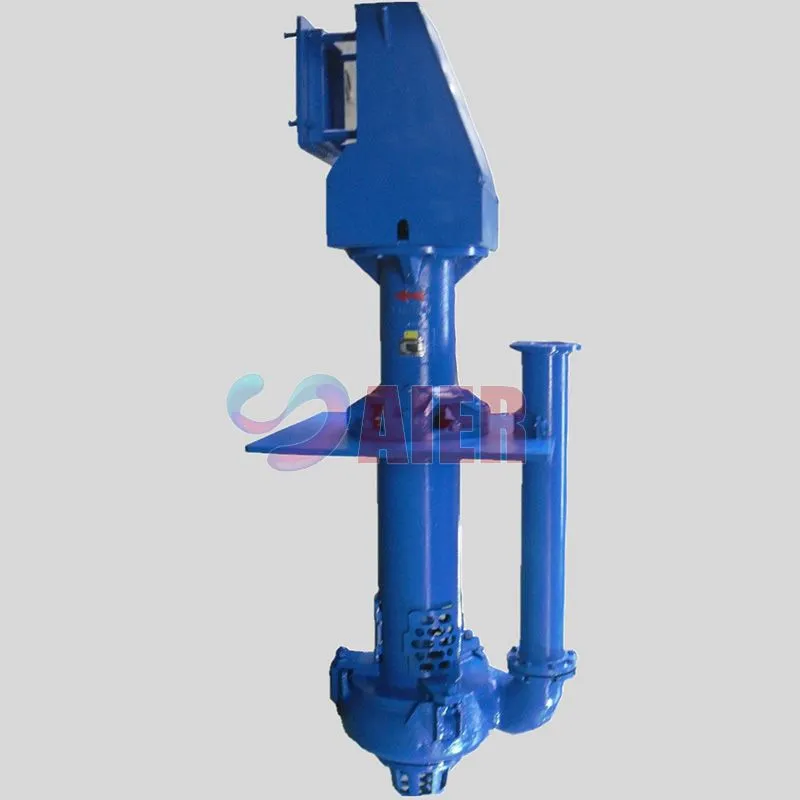
In industries where material handling involves abrasive and corrosive slurries, maintaining the efficacy and lifespan of equipment is paramount. Rubber lined slurry pumps have emerged as a reliable solution, offering enhanced durability and efficiency. However, ensuring their optimal performance hinges on understanding and utilizing the right spare parts.
The intrinsic value of rubber lined slurry pumps lies in their robust design and ability to handle challenging environments. Unlike metal-lined counterparts, rubber linings offer superior abrasion resistance, especially in applications involving fine particles. This feature not only prolongs the life of the pump but also minimizes downtime, which is crucial in industries such as mining, mineral processing, and wastewater management.
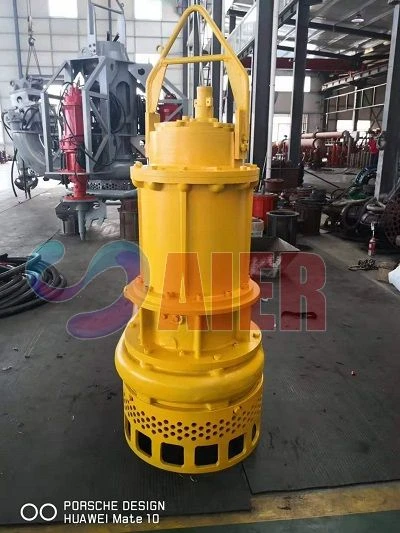
A pivotal factor contributing to the performance of these pumps is the quality and compatibility of the spare parts used. Selecting genuine spare parts specifically designed for rubber lined slurry pumps can drastically affect the operational efficiency and reduce maintenance costs over time. Therefore, delving into the specifics of these components is essential.
1. Pump Liners The rubber liners act as a shield between the pump casing and the slurry, absorbing shocks and reducing wear. Opting for high-quality linings ensures resistance against chemical degradation and thermal variations. Using advanced compounds like natural rubber guarantees elasticity and resilience, allowing the pumps to sustain optimal performance under high-pressure conditions.
2. Impellers The impeller's material and design can significantly influence the pump's capacity and efficiency. A rubber coated impeller can handle abrasive particles without succumbing to wear quickly. Engineering experts recommend considering factors like particle size and slurry pH when selecting impellers to ensure compatibility and prolong the device’s operational life.
rubber lined slurry pump spare parts
3. Seals and Gaskets Effective sealing is crucial to prevent leakage and contamination. Rubber seals and gaskets must be meticulously crafted from materials compatible with the slurry's chemical composition. Regular checks and replacements of these parts can prevent catastrophic failures and maintain the system’s integrity and safety.
4. Shaft Sleeves and Bearings The interaction of moving parts within slurry pumps places a substantial load on the bearings and shaft sleeves. Wear-resistant rubber sleeves safeguard the shaft from corrosion and abrasion. Additionally, selecting high-grade bearings tailored for slurry pumps enhances load capacity and reduces rotational friction, promoting a smooth operation.
5. Casings While the external casing of a pump is often metal, the interior is lined with rubber to protect against the harshness of slurry. It’s imperative to regularly inspect these casings for signs of wear or damage. Replacement with high-quality rubber casings can avert unscheduled downtimes and offer better protection than conventional metal casings.
Implementing a strategically planned maintenance schedule that incorporates regular inspections and timely replacements of these spare parts plays a critical role in sustaining the efficiency of slurry pumps. Furthermore, collaborating with reputable suppliers who offer certified parts ensures authenticity and reliability.
In conclusion, the selection and maintenance of rubber lined slurry pump spare parts are integral to optimizing equipment performance. Leveraging expertise in this domain, alongside a robust quality assurance framework, can dramatically improve operational efficiency, minimize costs, and extend the lifespan of these critical industrial tools. Businesses that prioritize investment in high-quality, compatible spare parts will invariably reap the benefits of enhanced productivity and reduced maintenance challenges, positioning themselves favorably in a competitive marketplace.