High quality slurry pump rubber is a vital component in a multitude of industries, particularly those involving harsh and abrasive environments like mining, mineral processing, and wastewater management. The rubber lining in these pumps must withstand severe operational conditions while providing longevity and reliable performance. As an industry expert with years of experience working with slurry pumps, I understand that selecting the right rubber material is crucial for reducing maintenance costs and enhancing efficiency.
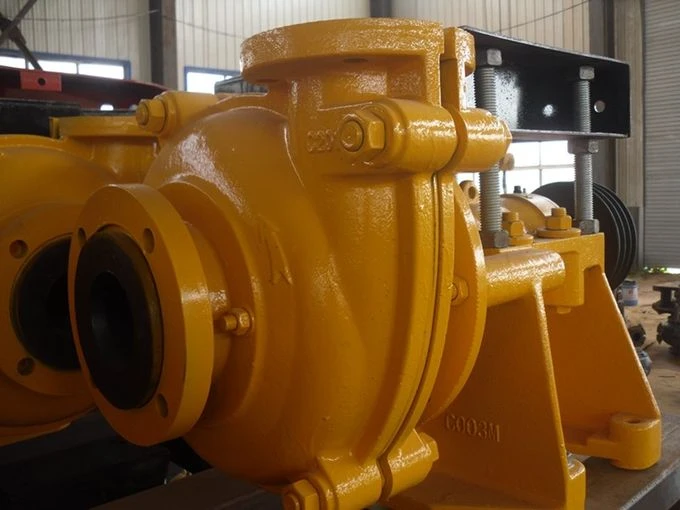
The first thing to consider in slurry pump rubber selection is the composition of the slurry itself. High-density slurries with coarse particles require robust rubber with excellent tear and abrasion resistance. Natural rubber and synthetic elastomers like neoprene and SBR (styrene-butadiene rubber) are often preferred due to their superior wear resistance and flexibility. Their molecular structures allow them to absorb and withstand the kinetic energy of abrasive particles, minimizing wear and tear.
From an expertise perspective, the manufacturing process of slurry pump rubber also contributes significantly to its quality. Injection molding and precision cutting technologies facilitate the creation of durable rubber parts that fit the pump perfectly. These cutting-edge techniques ensure that the rubber is evenly distributed and maintains uniform thickness, critical factors that affect the pump's performance and longevity.
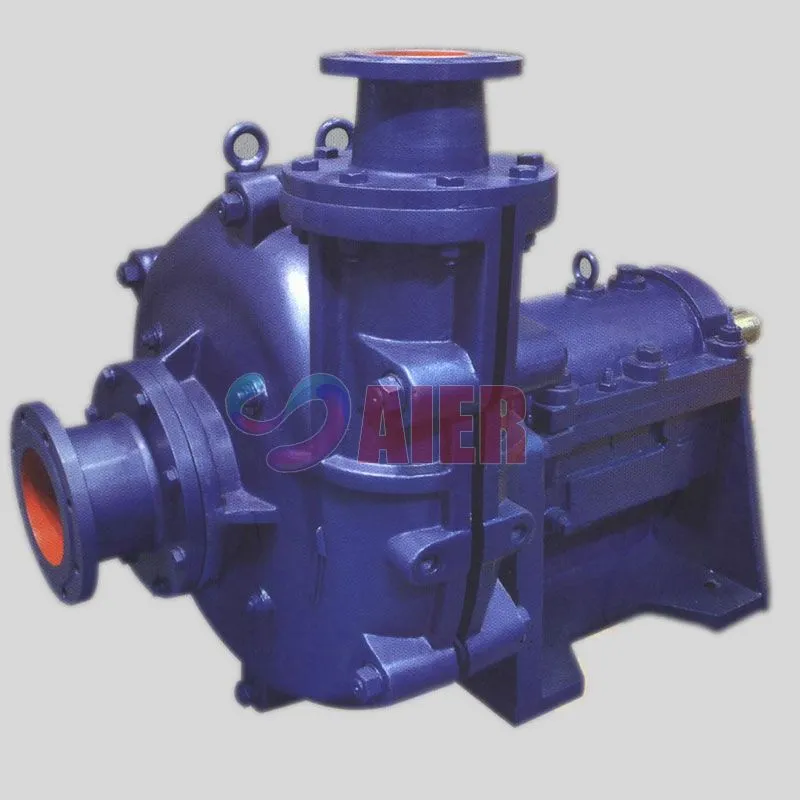
Authoritativeness in the industry is often demonstrated by adhering to international quality standards. ISO certifications, for instance, are an indication of a manufacturer's commitment to quality production processes. Furthermore, partnering with suppliers who provide detailed documentation and testing reports can help confirm the quality and suitability of the rubber for specific applications. This level of rigor and documentation builds confidence in the product's reliability.
high quality slurry pump rubber
Trustworthiness is, without doubt,
a crucial aspect when choosing slurry pump rubber. Field testing and real-world validations can provide insights not captured in a lab. Companies that share case studies or testimonials from clients who have used their rubber components effectively run campaigns of transparency and reliability. These stories confirm that the products perform as described, solidifying trust in the manufacturer and the product's capabilities.
In practical terms, the lifecycle cost of slurry pumps is largely influenced by the longevity and efficiency of the rubber lining. High-quality rubber components can extend the operational life of the pump, reduce downtime, and cut down long-term operational expenses. This is why it is essential to evaluate the performance history of the rubber in different applications and operational contexts, which can often be found in detailed product reviews or technical sheets provided by the manufacturer.
For industries aiming to optimize their operations, investing in high-quality slurry pump rubber is non-negotiable. The upfront cost may be higher, but the payoff in terms of reduced maintenance and enhanced efficiency is substantial. As a result, the decision should be guided by both technical specifications and case-based evidence that confirms real-world performance.
In conclusion, high-quality slurry pump rubber is paramount for ensuring that pumps operate efficiently under demanding conditions. By focusing on the material composition, manufacturing quality, adherence to established standards, and real-world performance verification, industries can make informed decisions that bolster operational reliability and cost-effectiveness. The right choice not only safeguards the equipment but also enhances the overall productivity of industrial processes, firmly supporting the premise that quality investment reaps sustainable rewards.