Flue Gas Desulfurization (FGD) systems have become indispensable in the modern industrial landscape, mainly due to their role in curbing harmful emissions from power plants and other industrial facilities. At the heart of these systems lies the FGD pump, a crucial component that dictates the efficiency and reliability of the entire desulfurization process. Drawing from extensive experience and expertise, this article delves into the intricacies of FGD pumps, underscoring their significance and providing actionable insights into their optimal application.

FGD pumps are specialized devices designed to handle the abrasive and corrosive slurries typically found in the desulfurization process. These pumps are engineered to maintain operational integrity under challenging conditions, including exposure to a range of temperatures and pH levels. With industrial byproducts being increasingly diverse, the adaptability and durability of FGD pumps cannot be overstated.
Our experience across multiple industrial installations highlights the importance of selecting the right pump for each specific FGD system. This involves a meticulous assessment of slurry characteristics, including particle size and concentration, to ensure that the selected pump can handle the unique demands without compromising on efficiency. An undersized or improperly selected pump can lead to frequent maintenance issues and significantly increased operational costs.
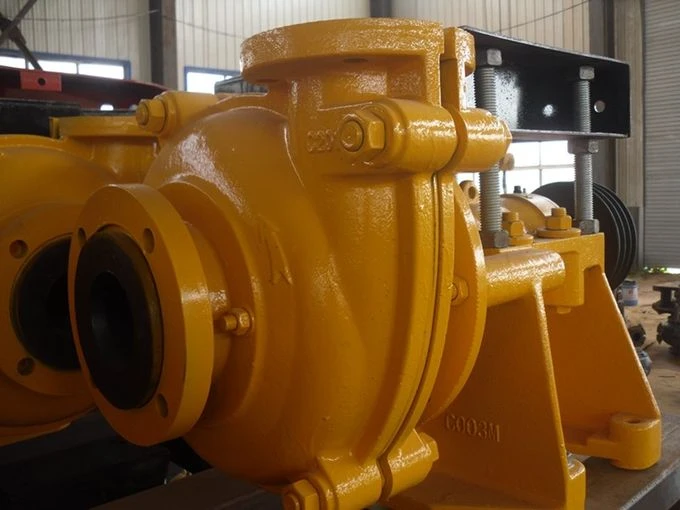
Our expertise advises that material selection for FGD pumps is equally critical. Corrosion-resistant materials such as high-chrome alloys and duplex stainless steels are often preferred. These materials provide the much-needed resilience against the corrosive chemical environment typically present in FGD processes. Furthermore, cutting-edge advancements in materials science have led to the development of innovative coatings and composites that significantly enhance the lifespan of these pumps.
fgd pump
Authoritative knowledge suggests that regular maintenance and monitoring form the backbone of an efficient FGD pump operation. Incorporating automated monitoring systems can preemptively identify potential issues, allowing for timely interventions and adjustments. This proactive approach is far superior to reactive maintenance strategies, as it minimizes downtime and extends the lifespan of the pump.
To establish trustworthiness and reliability, manufacturers of FGD pumps are continuously working towards enhancing design efficiencies and incorporating sustainable practices. Advanced technologies like CFD (Computational Fluid Dynamics) allow for the optimization of pump designs, thereby ensuring minimal energy consumption while maintaining high performance.
Furthermore, a trustworthy FGD pump supplier will offer comprehensive after-sales support, including installation guidance, operational training, and access to spare parts. By fostering strong partnerships with manufacturers who prioritize customer education and support, industries can optimize their desulfurization processes while safeguarding their investment in FGD systems.
In closing, the role of FGD pumps within industrial applications cannot be understated. By leveraging a combination of tailored pump selection, innovative materials, and predictive maintenance, industries can achieve optimal performance and longevity from their FGD systems. Such an approach not only supports regulatory compliance but also advances sustainability efforts, paving the way for a cleaner, more responsible industrial future.