Understanding and effectively managing slurry pump impeller wear is crucial for maintaining the efficiency and longevity of equipment in industries such as mining, dredging, and mineral processing. Slurry pumps handle abrasive mixtures that contain solid particles suspended in liquid, subjecting pump components, especially the impeller, to significant wear and tear. By harnessing professional experience, leveraging expertise, and building authoritative insights, we can navigate this complex topic with confidence.
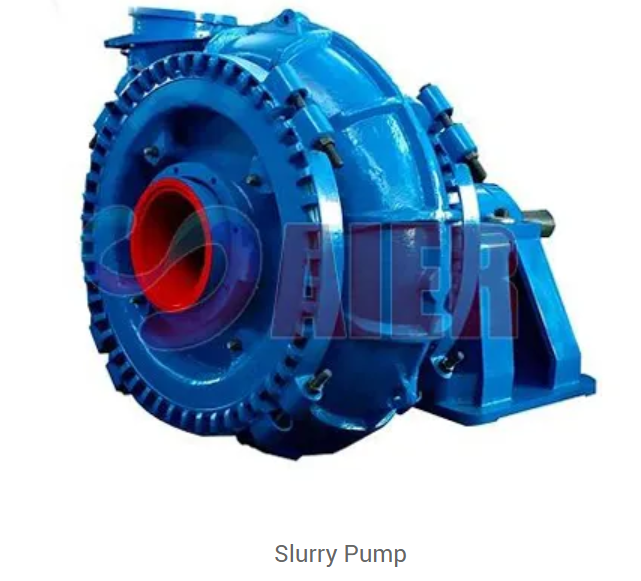
Slurry pump impeller wear predominantly results from three kinds of abrasive mechanisms sliding, impact, and erosion. Each mechanism affects the impeller differently, demanding distinct approaches for mitigation. Sliding wear occurs as solid particles rub across surfaces, gradually removing material. This can be visualized similarly to sandpaper grinding against wood. Impact wear, in contrast, happens when particles strike the impeller at high velocities, chipping away at the surface. Erosion wear, often the most challenging, involves particles entrained within the fluid destroying surfaces as they move along turbulent paths.
Through extensive practical experience, professionals understand that the material composition of impellers plays a pivotal role in resistance against wear. High chrome alloys, elastomers like rubber, and increasingly sophisticated ceramics have been employed to combat the destructive nature of slurry abrasives. High chrome alloys, renowned for their hardness and resistance to sliding wear, are a staple in combating coarse particle abrasion. Elastomers, while less durable against sharp impacts, excel when particles are finer and slicker, reducing erosive potential. Ceramics, though more brittle, prove highly effective in scenarios involving extreme temperatures and finely pulverized slurries.
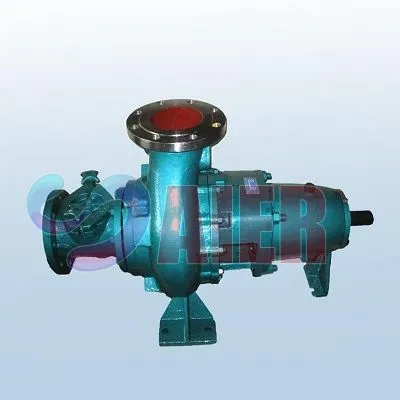
The choice of impeller geometry is another expert consideration. Closed, semi-open, and open impeller designs each offer distinct advantages depending on the slurry type. Closed impellers provide enhanced efficiency and reduced wear for slurries with lower solids concentrations. Semi-open designs adapt to fibrous and larger particulates, while open impellers, though more susceptible to wear, allow for easy passage of large, coarse solids.
slurry pump impeller wear
Operational practices are equally influential in minimizing wear on slurry pump impellers. Proper pump selection, regular preventative maintenance, and operational adjustments based on real-time data feedback can extend the lifespan of impellers significantly. In practice, aligning the Best Efficiency Point (BEP) with operational needs prevents excess strain on the pump, reducing wear rates. Similarly, advanced monitoring tools, such as vibration analysis and ultrasonic testing, offer insights into wear patterns and impending failures, allowing preemptive action.
One cannot ignore the importance of trust and authority in discussing slurry pump maintenance. Industry leaders and experts build authority through consistent performance, innovation, and collaboration with trusted material suppliers and technical advisers. The community thrives on shared knowledge and validated techniques, promoting collective trust. Published case studies, peer-reviewed research, and involvement in professional associations serve as pillars reinforcing the credibility of suggested wear management strategies.
Investing in training and development for operational staff further cultivates a trustworthy environment. Employees, trained to recognize early signs of impeller wear and understand corrective procedures, can prolong the life of pump components and ensure operational continuity.
Ultimately, a comprehensive approach to managing slurry pump impeller wear integrates material science, operational finesse, and authoritative practices. It involves a multifaceted strategy encompassing the selection of suitable materials and designs, proactive maintenance, and leveraging real-time data analysis. Through meticulous attention to detail and expert knowledge, it is possible to significantly mitigate impeller wear, thereby enhancing the reliability and efficiency of slurry pumping systems.