Enhancing Slurry Pump Performance with Wetted Parts in Factories
In the dynamic world of industrial pump manufacturing, the demand for high-efficiency and durable slurry pumps continues to surge. A critical aspect that determines a slurry pump's longevity and effectiveness is the quality of its wetted parts. These components are in constant contact with abrasive slurries, making them prone to wear and tear. In this article, we will explore how factories can leverage advanced wetted parts to boost their slurry pump performance.
The heart of any slurry pump lies in its wetted end—the impeller, casing, and wear plates. These parts must endure the relentless onslaught of solid particles suspended in liquid. Over time, conventional materials used in these parts can degrade, leading to increased downtime and repair costs. However, by incorporating cutting-edge materials science into wetted part design, factories can unlock unprecedented levels of pump reliability.
Ceramic composites and super-hard alloys have emerged as game-changers in the realm of wetted parts. These materials boast superior hardness and resistance to corrosion, reducing the frequency of replacements. For instance, tungsten carbide, with its exceptional hardness, can withstand even the most abrasive slurries, significantly extending the service life of wear plates and impellers For instance, tungsten carbide, with its exceptional hardness, can withstand even the most abrasive slurries, significantly extending the service life of wear plates and impellers
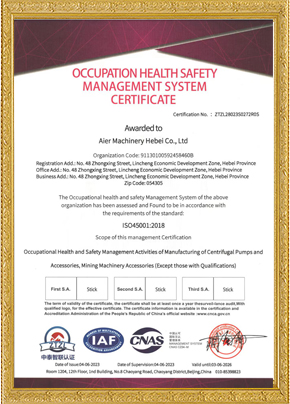
For instance, tungsten carbide, with its exceptional hardness, can withstand even the most abrasive slurries, significantly extending the service life of wear plates and impellers For instance, tungsten carbide, with its exceptional hardness, can withstand even the most abrasive slurries, significantly extending the service life of wear plates and impellers
wetted parts for slurry pump factories.
Moreover, factories are adopting surface coating technologies to enhance the durability of wetted parts. Coatings like titanium carbide or diamond-like carbon (DLC) provide an additional layer of protection against abrasion and erosion. By applying these coatings to critical components, manufacturers can achieve significant improvements in pump efficiency and longevity.
Another innovative approach is the use of smart monitoring systems that track the condition of wetted parts in real-time. Through sensors embedded within the pump, data on temperature, pressure, and particle concentration can be analyzed to predict potential failure points. This proactive maintenance strategy allows factories to schedule repairs during planned downtimes, minimizing unscheduled stoppages.
In conclusion, the integration of advanced wetted parts into slurry pump designs represents a strategic investment for factories. By embracing innovative materials, coatings, and monitoring technologies, manufacturers can ensure their pumps operate at peak efficiency while reducing maintenance costs. As the industrial sector continues to evolve, the optimization of wetted parts will undoubtedly play a pivotal role in shaping the future of slurry pump manufacturing.